インターフェイスの DLC コーティングは、優れた 耐摩擦性、耐磨耗性、低摩擦係数、装飾等幅広い用途で付加価値を提供し、15年以上になります。
DLC コーティングは他の硬質膜に比べ、圧倒的に低い摩擦係数と、優れた耐擬着性、耐摩耗性を示します。
特に電子部品に多く用いられ、銅(銅合金)やインコネル、はんだメッキ品の加工に優れた威力を発揮し、
曲げ、切断用のダイやパンチ、さらには位置決めピン搬送用ガイドにも用いられます。
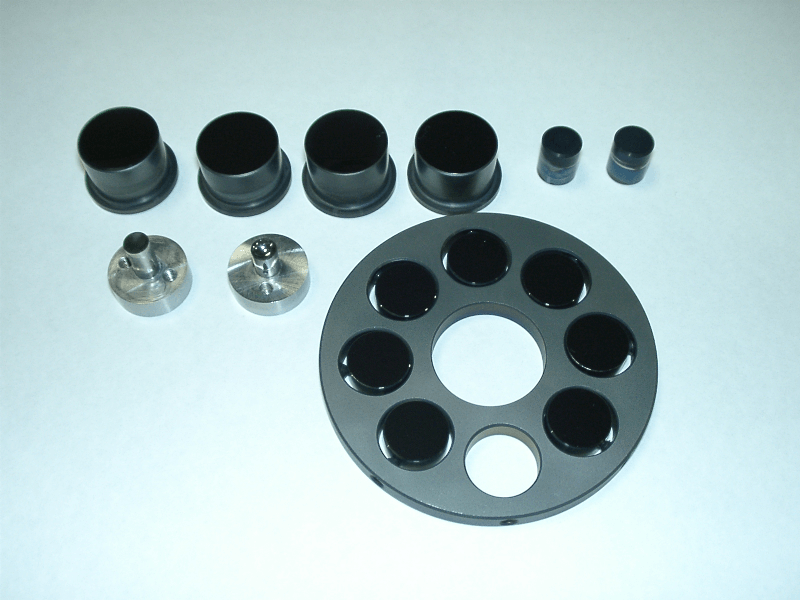
- 膜厚:1μm
- 硬度:3000-5000HV
- 摩擦係数:μ=0.1
- 処理温度:200℃
- 比抵抗(Ωcm): 106;〜1012
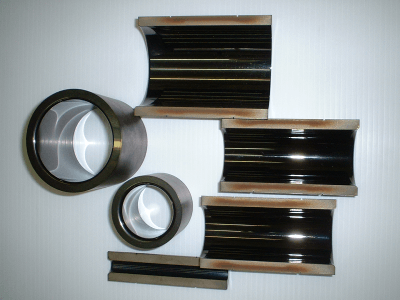
DLC内径コーティング
応用製品一覧
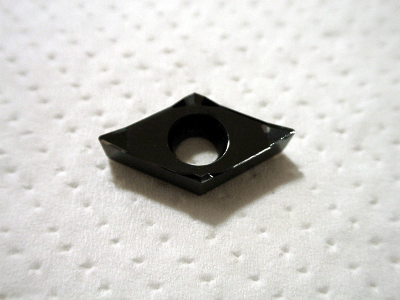
超硬 切削チップ
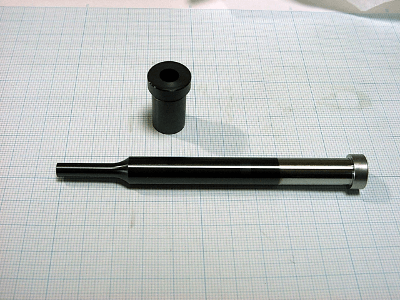
打錠 杵臼
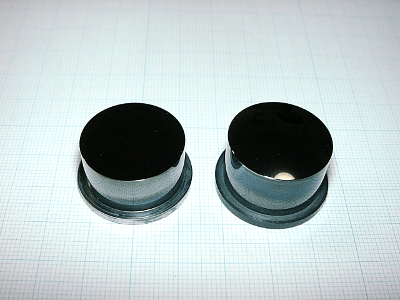
レンズ 金型
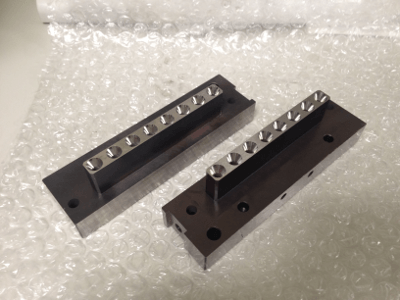
部品 耐磨耗用
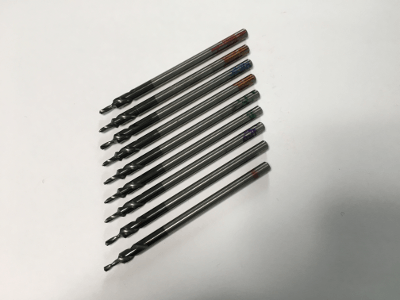
超硬 切削ドリル
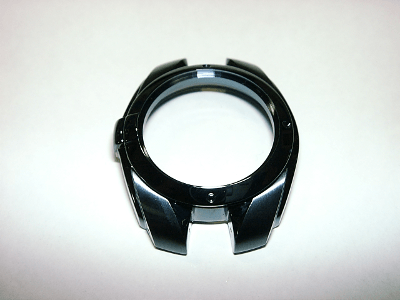
時計 フレーム
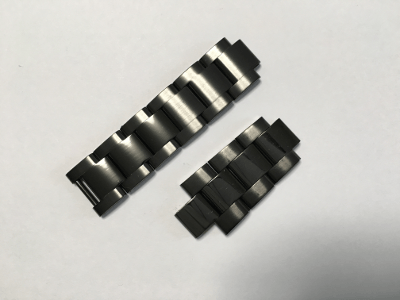
時計 バンド
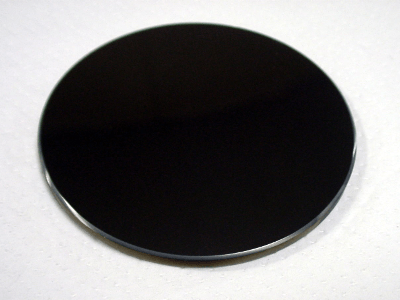
部品 円盤
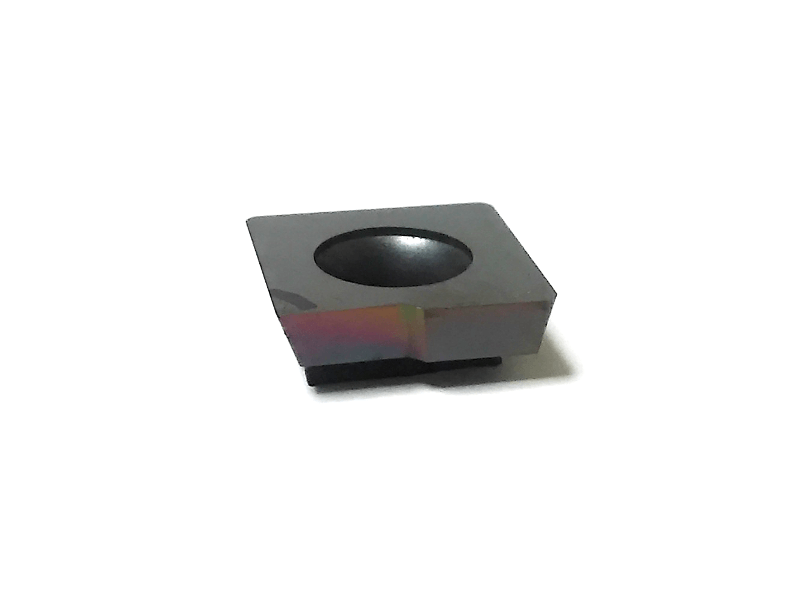
切削工具
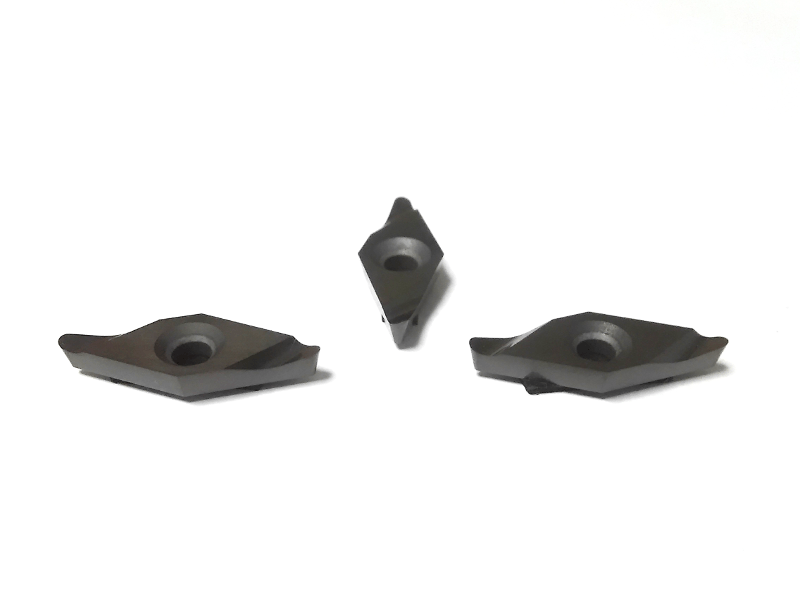
インサート
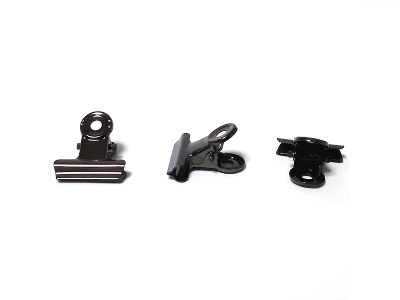
クリップ
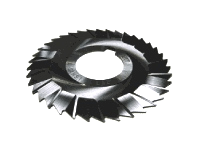
丸ノコ刃
特性
- 低い摩擦係数
- 摩擦係数が低い(μ=0.1)ため、衝動性 が向上し高い潤滑特性が期待できる。
- 高い硬度
- 硬度がHv3000〜5,000あり、ダイヤモンドに近い硬さを持つ。
- 薄い膜
- 膜厚1ミクロン(数十ナノの超薄膜も可能)厚膜対応可能
- 剥離処理
- プラズマエッチング処理で、膜の除去が可能。再生が容易である。
DLCコーティング工具による切削結果
(1)アルミニウム合金鋳物のドリル切削
切削条件 |
試験結果
|
|
超硬無処理 | 超硬(K10)DLC処理 | |
乾式切削速度: φ5.5 V=100m/min 回転数: N=5800min-1 送り量: f=0.082mm/rev 送り速度: F=480mm/min |
28穴で折損(溝面の凝着が著しく切りくず詰まりによる) | 3567穴超、継続切削可能 (凝着は殆ど見られず) |
(2)アルミニウム合金A5052圧延板のドリル切削
切削条件 | 試験結果 | |
---|---|---|
超硬無処理 | DLC処理 | |
湿式切削速度φ5.5: V=100m/min 回転数: N=5800min-1 送り量: f=0.08mm/rev 送り速度: F=480mm/min 穴深さ: L=27.5mm止り穴 アスペクト比: L/D=5 |
1570穴で折損 | 10400穴超、継続切削可能 穴径拡大量±0.02mm マージン部への凝着による 穴径拡大見当たらず |
(2)アルミニウム合金A5052圧延板のエンドミル切削
切削条件 | 試験結果 | |
超硬無処理 | DLC処理 | |
乾式 φ10 立形フライス盤 切削速度 V=314m/min 回転数 N=10000min-1 送り速度 F=1000mm/min 1刃当たり送り fz=0.05mm/刃 切り込み Ad=15mm |
早期折損 (外周刃の凝着が大きく、 切りくず詰まりによる) Ry=31.5μm |
折損なし (凝着軽微、加工面にむれなく良好) Ry=4.55μm |
青木正義 著、「現場で役立つプラスチック金型技術」、工業調査会出版 より
DLCの特性と応用
1.はじめに
硬質薄膜が市場に出始めてはや25年がたちます。その技術革新には目覚ましいものがあり、今は誰でも目にするようになってきています。みなさんご存じのTiN(窒化チタン)は硬度もHv2300と硬く色も金色である為、装飾品にも使用されます。その用途は広く、切削工具 金型 摺動部品 時計からゴルフでお馴染みの、磁気ブレスレットやゴルフクラブにも採用されています。
最近、少量多品種の時代になっておりますが、コーティングの世界にもこの波が押し寄せてきています。各ユーザーがTiNでは飽き足らなくなってきたのか?(おかげでDLCの商売が成り立っている訳ですが)用途に合わせた多種の膜が出てきています。例えば、TiN TiC TiCN TiCNO TiAlN TiCrN CrN CrC DLC等膜種が多くユーザーの方も困惑していることと思います。
2.成膜技術
この様な薄膜(表面改質技術)は、次の理由から真空を用いたドライコーティングが広く用いられています。
- 公害を発生しない
- 成膜材料が少量(省エネ)
- 膜種が豊富(金属、セラミック、プラスチック)
- 相手材が豊富(金属、セラミック、プラスチック)
- 膜の構造(性質)を変えられる
- 高純度膜が得られる
蒸着方法
物理蒸着法PVD | 真空蒸着 スパッタリング イオンプレーティング イオンビーム蒸着 イオンミキシング |
---|---|
化学蒸着法 PVD |
熱CVD 減圧CVD プラズマCVD |
蒸着方法には、下記表に示す様に大きく2つに分類されます。簡単に言えば、被膜構成物質を蒸発させて品物に膜付けする方法を物理蒸着、被膜構成物質を含むガスから膜を析出(化学反応)させる方法を化学蒸着CVDと分類する。具体的に言えば、チタンを溶かし蒸発させ窒素ガスを入れてTiNとするのがPVD、四塩化チタンガスと窒素ガス、水素ガスからTiNを合成するのがCVDである。
(TiCl4 + 1/2N2 +H2 = TiN +4HCl)
CVDとPVDの比較
CVD | PVD | |
---|---|---|
材料 | 生成物構成元素からなる化合物の気体 | 生成物の蒸気及び構成成分の蒸気 |
活性化法 | 温度上昇による方法を主とし低温化の為これに付加的にプラズマ、光、レーザー、高周波などの高密度化エネルギーを使用 | 蒸発熱や蒸発エネルギーを主としてプラズマ、バイアス電圧、イオン化エンネルギーなどを付加的に使用 |
基板温度 | 150℃〜2000℃ | 25℃〜550℃ |
成膜速度 | 2nm〜500nm/sec | 1nm〜100nm/sec |
3. DLCとは
ダイヤモンドライクカーボンを略してDLCと呼んでいますが、その名前の示す様にダイヤモンドに似たカーボン膜ということで、ほとんど定義化されていません。DLCは1970年頃に世の中にでましたが、その後気相合成ダイヤモンド(多結晶ダイヤ)の影に隠れ、にせダイヤと言われ研究する人も少なくなりました。
しかし最近、気相合成ダイヤモンドでは限界があることが分かり、DLCに期待が集まり研究者も増えてきました。ここで気相合成の限界というのは、高温(600℃以上)であることを意味します。成膜エリアが狭い多結晶であるため表面粗さが悪い(数μm〜数10μmの粒の集まり)の問題があり実際母材の制約、用途の制限、高価である欠点を持ちます。DLCはこれに比べ、低温処理である(25℃〜200℃)、適応母材範囲が広い(プラスチックへも可能)、大面積化が容易である(2002年現在400×2000L)の利点をもち用途が拡大している。DLCはアモルファスダイヤモンドの別名をもつ様に、結晶をもたないため、非常に平滑な表面状態を作れる、非常に硬い(Hv5000)、摩擦係数が低い(よく滑る)、相手を攻撃しないと優れた利点を持ちます。
# | DLC | ダイヤモンド | TiN |
---|---|---|---|
結晶構造 | アモルファス | 多結晶 | 多結晶 |
構成元素 | C,H | C | Ti,N |
硬さHv | 3000〜5000 | 〜10.000 | 2,000〜2500 |
表面粗さRa | <0.1μm | 5〜10μm | <0.1μm |
色調 | 黒色(0.8μm以上) | 灰色〜半透明 | 黄金色 |
電気特性 | 106〜1014Ωcm | 1014〜1016Ωcm | 10-5〜10-4Ωcm |
光学特性 | 赤外域で透明 | 赤外域で透明 | >赤外線反射 |
化学特性 | 酸、アルカリに対し安定 | 酸、アルカリに対し安定 | 酸に対し安定 |
DLCの基本特性は、すばらしい物がありますが、その反面欠点もあります。
- 硬すぎる、これは硬いが為脆い、割れやすいという問題。
- 残留圧縮応力が大きい為、最大膜厚が限定される。
- 応力が大きい為密着強度の確保が難しい
- 耐熱温度が450℃である。実際には300℃から、グラファイト構造に移行し始める。炭素の膜なので酸素に弱い。
この問題を克服する事が、DLCの課題であるが適切な素材、適用される用途を選定することも重要である。金型や治工具の材質は、
超硬(最も適する)> SKH > SKD である。
では、他材料にはDLCコートは不適当なのか?
SUS304 SUJ2 STAVAX アルミナ ポリイミド PET など多くのものに適応されている。つまり用途の選定が大事なのである。
DLCの特性を生かした使用方法、すべり特性、離型性、化学的安定性、電気特性を重要視した使い方では数多く成功している。
4. 成膜プロセスと装置
私どものDLCは、PVD(イオンプレーティング)方式と、CVD方式の2種類で成膜できます。PVD方式は、原料として炭化水素系のガス体を用いるため、CVDと思われがちですが、成膜時の圧力が10-4〜10-3Torr台と中真空領域であり、イオンガンを用いる為、プラズマ発生空間と成膜空間の区別が比較的明確であり、かつイオン運動エネルギーの効果が大きいことから、プラズマCVDではなくイオンプレーティングに分類されます。
イオンプレーティングによるDLCは、図1のイオンガンを用いて成膜します。原料は炭化水素系ガスを使用し、イオンガンでプラズマを発生させガスを分解イオン化します。イオン化したガスは、CxHy+の状態になり基板バイアス(-)に引き込まれ(加速され)基板上(製品)でDLC(C-H)となります。このイオンガンを量産装置では、4台装備しており(図2参照)エリアの拡大と成膜時間の短縮ができます。また量産装置では、自公転治具を装備しており均一なコートができます。